MJP –
A 25-year-old worker who once manufactured components for trash trucks is a key component in the Navy’s capacity to construct more affordable vessels capable of intercepting Houthi rebel rockets in the Red Sea.
In the wake of shipyards’ hiring and retention crises, thousands of young workers, like Marinette, Wisconsin’s Lucas Andreini, have benefited from employer-sponsored training programs around the country.
In the midst of growing global threats, the Navy is experiencing delays in ship building and upkeep due, in part, to a lack of available workers. The United States is falling further and further behind China in terms of the number of ships it has available, a situation exacerbated by changing defense priorities, last-minute design revisions, and budget overruns.
According to Eric Labs, a veteran naval analyst at the Congressional Budget Office, the present situation of navy shipbuilding is “a terrible state” – the worst in twenty-five years. “I am very worried,” he expressed. “As far as I can tell, there is no simple solution to this situation. We’re finally getting into it after a long delay.
Six guided-missile frigates, the most recent surface warships in the Navy’s fleet, are now under construction at Marinette Marine, with an additional four construction slots available. Labs claim that the company can only manufacture one frigate every year because of a lack of personnel.
The workers have mysteriously vanished.
As the industry’s graying veterans retire, bringing decades of experience with them, one of the main difficulties is the effort to hire and retain workmen for the challenging work of building new ships.
To equip its workforce with the necessary skills to build state-of-the-art warships, shipyards across have established training academies and formed partnerships with technical institutions. The Navy and submarine builders have joined forces to encourage manufacturing jobs, and shipyards are providing incentives to keep employees.
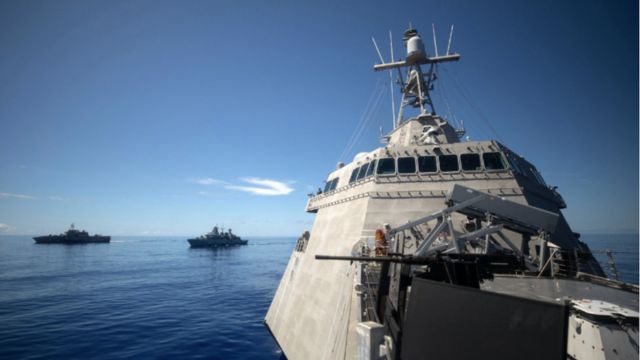
Thanks to a curriculum at Northeast Wisconsin Technical College, Andreini was prepared for his work at Marinette. He had previously worked as a welder on a production line for several years, creating parts for garbage trucks. The perception that shipbuilding is a “crappy work environment, and it’s unsafe” is preventing some of his friends from pursuing the career path, he claimed.
However, he insisted that this was not the case. In addition to improved health benefits compared to his prior work, he will be eligible for a pension for the first time, and he has the chance to upgrade his training even further.
Plus, according to Andreini, he has a strong sense of patriotism.
SEE MORE –
US Military Deploys Reinforcements to the Middle East Amid Rising Tensions
Andreini mentioned that it brings her joy to be able to contribute and perhaps ensure the safe return of service members and sailors, as her father served in the Navy in Vietnam.
Another welder and fellow program alumna of the technical college, Alonie Lake is a single mother who is grateful for the security that Marinette’s backlog of Navy contracts provides.
“And the satisfaction of working with their hands to create tangible results” is what attracts many young people to trades employment, according to Lake, 32.
During the recent commencement ceremonies at a community college in Maine, Navy Secretary Carlos Del Toro emphasized the significance of training programs. To train people to fix nuclear submarines, the college has teamed up with the adjacent Portsmouth Naval Shipyard.
He emphasized that everyone should think about how they might contribute their skills and abilities, especially the graduates’ newly acquired knowledge, to strengthen the United States of America for future generations and to combat current difficulties and threats.
Will employees remain once hired?
With the labor market being so tight, the Navy is attempting to assist shipyards in keeping their newly educated and hired employees.
The shipyard’s previous staff retention rate was characterized by Del Toro as “atrocious,” and a portion of the $100 million in Navy funding going to Marinette Marine in Wisconsin is going toward retention bonuses.
A spokeswoman for the shipyard, Eric Dent, claimed that bonuses of up to $10,000 are being offered to employees to retain them. The shipyard employs over 2,000 people. Everyone in the shipyard industry is feeling the pinch from the labor crisis, he added.
Shipyards like Huntington Ingalls Industries, which manufactures destroyers and amphibious vessels in Mississippi and aircraft carriers and submarines in Virginia, nevertheless face retention challenges even after reaching their goals.
Colleges and public schools across all grade levels are joining forces with the industry to form training partnerships. Improvements in Mississippi include a second dining room with a Chick-fil-A, hydration stations, and a covered work area that exceeds one million square feet (92,900 square meters). To accommodate employees and sailors, Huntington Ingalls worked with the Navy and the city of Newport News, Virginia, to construct a new parking garage.
An issue that has persisted for many years
It is the Navy’s habit of making last-minute modifications to specifications, requests for enhancements, and design adjustments that is largely to blame for the present state of U.S. shipbuilding.
Some examples of this include the early retirement of some of the Navy’s lightly armored littoral combat ships due to their high maintenance costs and the cost overruns, technological challenges, and delays experienced by the newest aircraft carrier, the USS Ford. Another example is the spiking of a gun system for a stealth destroyer program, which occurred when the program’s rocket-assisted projectiles became too expensive.
The Navy has promised that the new frigates being constructed at Marinette Marine will take into account those previous mistakes. The frigates’ comparable weapon systems make them desirable, and their lower production costs make them more affordable than larger destroyers.
The navy opted not to start from scratch but instead to use a ship design that was already in service by the fleets of France and Italy. To keep costs down and building times down, the plan was to alter 15% of the vessel to conform to U.S. Navy regulations while leaving 85% intact.
According to Bryan Clark, an analyst at the Hudson Institute in Washington, the Navy modified 85% of the ship, which led to increased costs and construction delays. The first-in-class Constellation battleship has been delayed from its original 2022 delivery date to 2029, a three-year delay.
We haven’t finished the final design yet.
Altering dangers and evolving strategies
An additional factor is the ever-evolving character of global threats, which is beyond the control of the Navy.
The Navy has had to change and adapt to different dangers throughout the years, from the Cold War to the present day, when there is war in the Middle East, rising rivalry from the navies of China and Russia, Somali coast piracy, and repeated assaults on commercial ships in Yemen by Houthi rebels.
Oh, and there’s more. According to Matthew Paxton of the Shipbuilders Council of America, a national trade body, the rhythm of ship construction has been disturbed and long-term investments and planning have been impeded due to financing difficulties and the concentration of shipyards.
Uneven shipbuilding plans have plagued the company for years, according to Paxton. “The loss of personnel surprises the Navy when we begin to ramp up.”
The Navy maintains its stance that the shipbuilding issues are being dealt with carefully.
The significance and breadth of the Navy’s role in protecting our country and fostering peace have never been greater, according to Lt. Kyle Hanton, who addressed on behalf of Del Toro’s office. “We are committed to collaborating with our industry partners to find innovative ways to address the shared challenges we face.”